Sustainaweekly - Electrification of the dairy industry also makes financial sense
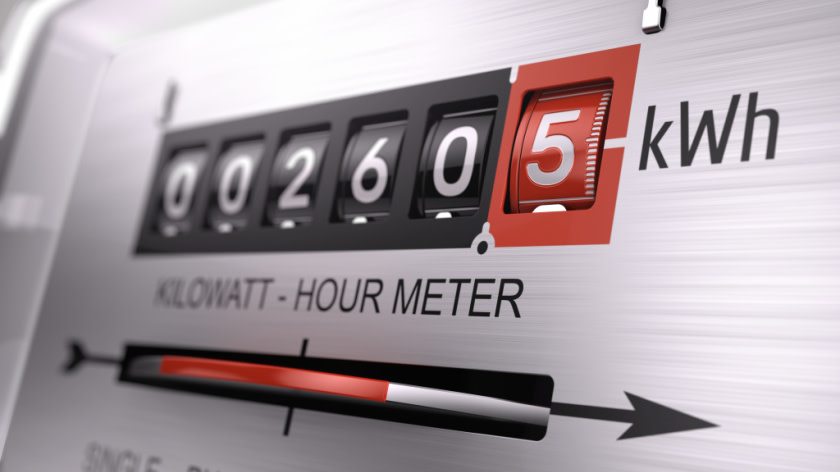
In this week’s SustainaWeekly, we take a closer look at the electrification of the dairy industry. Using data from the Dutch dairy company, Royal Friesland Campina, we try to quantify the benefits from a switch away from gas powered boilers, to electric ones. Electric boilers can prove to be a financially rewarding investment, and have also the benefit of acting as a low carbon technology. We also discuss the current usage of energy in the dairy sector, the source of the emissions within its production process and its cost structure. We then move to providing a short review of how the ESG bond market for financial institutions developed over the last quarter. We analyse whether the financial advantage of issuing ESG-labelled debt still holds in the primary market, and which ranks of debt have been mostly exposed to the rise of new issue premia.
Economist
Using Royal Friesland Campina’s published carbon emissions, we tried to estimate whether a switch from gas powered to electric boilers makes sense, both from a financial and sustainability perspective. We show that at existing natural gas prices such an electric boiler investment could be recovered by one year of savings in energy cost and gas prices would need to drop to EUR 78 MWh before the electric boiler solution becomes more expensive than the gas boiler.
ESG Bonds
We take a closer look at the ESG bond issuance by financial institutions in 2022 and in particular in the third quarter. Large volatility in the financial markets resulted in more ESG bond issuance, which was met with strong demand from investors. Nevertheless, new issue premia for those bonds was on the rise. This was particularly true for riskier ranks of debt.
ESG in figures
In a regular section of our weekly, we present a chart book on some of the key indicators for ESG financing and the energy transition.
Sustainable electrification in dairy industry
The diary processing industry can invest in energy efficiency, which yields relatively high returns at low risk
Electric boilers are efficient to use, but require a good connection and sufficient mains capacity
From Royal Friesland Campina’s published carbon emissions we were able to reverse engineer a business case for electric boilers
At existing natural gas prices such an electric boiler investment could be recovered by one year of savings in energy cost and gas prices would need to drop to EUR 78 MWh before the electric boiler solution becomes more expensive than the gas boiler
Sustainability is receiving a lot of attention within the Dutch dairy sector. The themes are diverse for the sector and for the entire value chain. Consider climate-responsible milk production, animal health and welfare, biodiversity and encouraging outdoor grazing. Within these themes, it is about maintaining high milk quality, safety, reduction of pesticides, minimum requirements for maximum greenhouse gas (GHG) emissions and sustainability through electrification instead of natural gas, for example. For dairy processors, with today's relatively high energy costs, having a plan for energy reduction and efficiency has become more of a priority. More electrification of the production process also helps to reduce GHG emissions from their own operations. But at the same time, this should also be a business-friendly option. In this note, we explore the use of electric boilers to replace (or, in better words, complement) natural gas as a sustainable option at dairy processing plants and showcase through Royal Friesland Campina’s data what potential financial and sustainability lie behind such a switch.
Energy usage and efficiency
The production process of dairy processing plants requires a lot of heat and steam. Heat treatment requires a relatively large amount of energy and steam is the main secondary energy carrier in the dairy industry. Typically, a lot of natural gas is consumed for this purpose. A variety of alternative sustainable methods can now be used to produce steam, such as electric boilers, biogas or green gas boilers, heat pumps or geothermal energy. The dairy industry is characterised by high consumption of raw materials and relatively low consumption of energy. To reduce GHG emissions, the sector can focus mainly on fuel substitution and process redesign for better results.
Investing in energy efficiency - if done properly - usually yields relatively high returns and the risks are usually low. Such an investment ultimately results in substantial savings on overall energy costs. Energy consumption in the dairy industry consists largely of natural gas (around 75%) and electricity (around 25%). The supply of natural gas and electricity to the diary processing industry increased by 2.7% and 0.8% year-on-year, respectively, in 2020. At the time of writing, 2021 figures regarding natural gas and electricity supply to the dairy industry were not yet available. Most likely, supply in 2021 for both natural gas and electricity will be at a similar level or slightly lower than corona year 2020, as in 2021 corona also had a significant impact on business activities as the out-of-home business segment was still confronted with lockdowns.
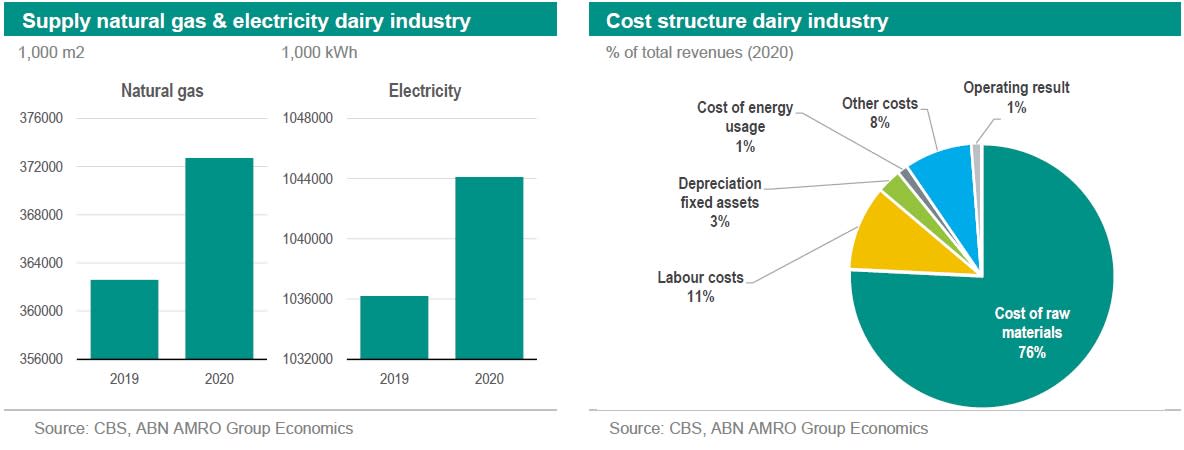
The sector is characterised by relatively high consumption of raw materials and relatively low consumption of energy. Thus, the cost of energy consumption in the dairy industry is only around 1% of operating income. Partly as a result, rising energy prices have not directly led to falling energy demand or deteriorating financial results.
Electrification of the production process mainly helps to reduce direct and partly indirect (that is, scope 1 and 2) GHG emissions. Reducing scope 1 and 2 emissions is the low-hanging fruit. For this, the sector has several technological options at its disposal. Our analysis focusses on these quick gains in direct energy usage, although we must admit that these have the least bearing on the diary industry’s total emissions. Indeed, reducing scope 3 emissions, which are largely tied to the dairy farm and make up a much bigger part of total value chain emissions, is considerably more complex. This is because they are more difficult to measure and control. Dairy processing companies will therefore continue to look at these upstream emissions as well as they contribute a lot to their scope 3 basket.
An electric boiler as low carbon technology
Most energy consumption in the dairy processing industry comes from the spray drying process to create powdered milk. This requires a lot of steam, which in many cases is produced using natural gas. Electric boilers can be used to decarbonise existing gas powered boilers used for heating purposes. Especially when the electricity used is produced entirely from a renewable energy source, it becomes a GHG-free source of energy.
Electric boilers are efficient in use. For instance, a boiler needs only a short time to reach full power. Moreover, it can be deployed in multiple ways. Besides being used in the energy intensive spray drying process, it can also be used for pasteurization or medium heat warming of milk to kill bacteria, provided that electricity prices are relatively low. The MIDDEN project by PBL and TNO () suggests that the investment in an electric boiler is between EUR 150-190 per kW. Maintenance costs are around EUR 1.10 per kW per year. An electric boiler is assumed to have an economic lifespan of 15 years. However, an obstacle is still that an electric boiler requires a proper grid connection and that sufficient grid capacity is available, but this strongly depends on the local infrastructural grid situation, government policy and grid operator expansion investments.
From carbon emissions to installation energy usage – Friesland Campina
To test the viability of electric boilers in the milk processing industry, we use Dutch diary company Royal Friesland Campina’s (RFC) proxied factory energy usage as an example. By comparing this energy usage with the cost of renewable electricity (for the electric boiler option) and gas (for the existing fossil fuel powered boiler), we should be able to conclude whether an investment in an electric boiler makes sense.
We get to the proxied factory energy usage by converting RFC’s reported emissions through standard emission factors. RFC reported in 2021 691 MT of carbon emissions related to factory & transport. All electricity requirements are fulfilled by zero carbon sources suggesting that the remaining emission are tied to natural gas and transport fuel. According to the company, 92% relates to the milk processing plants (factory) and 8% relates to transport. Hence, the factory’s emissions of 634MT (92% times 691MT) would come close to 355mn cubic metre of natural gas assuming 1.788kg carbon per one cubic metre of natural gas being used to heat the entire factory installations. 355mn cubic metre gas would require roughly 3474 GWh of electricity to achieve a similar level of heating.
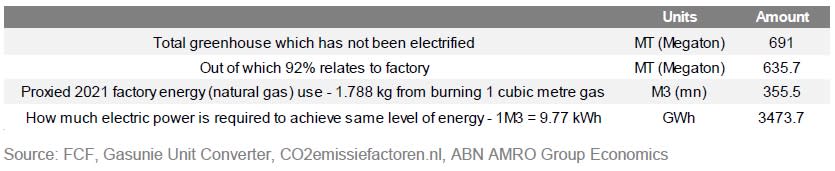
The main issue with the electric boiler is the intermittency of renewable electricity, as for example, on-shore wind turbines only operate 26% of the time on average (this is also known as the load factor). However, since RFC would like to have full boiler capacity being available when the renewables are churning out power, they would have to invest accordingly as if the renewables were operating at 100%. Assuming that the RFC factories operate 24/7 for 360 days per year (leaving some time for maintenance), the required thermal capacity for the electric boiler is 402 MW. Using the high range of EUR 190 per KW in capex, we get to EUR 76mn outlay for electric boilers. RFC reports EUR 7.6bn worth of gross property plant & equipment in its 2021 annual report, hence such a small investment will hardly require big capital allocation needs.
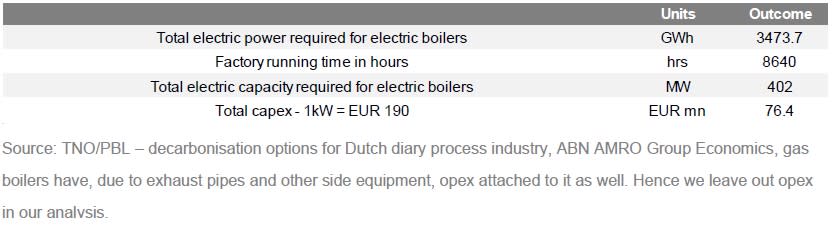
At the existing high gas price level the rewards for switching to electric boilers is very attractive, both financially and from a sustainability perspective
Now we try to compare the cost of the new installation against continuing the existing gas powered boilers. Regarding the cost of renewable electricity, we think a long-term contract (or PPA) would make sense. Pexapark (a PPA data provider) in its latest market update suggested that, although the current PPA market was currently illiquid due to stress in broad power markets, a 10y contract in Germany and the Netherlands would transact at EUR 98.5 and EUR 81.3 per MWh respectively (so roughly EUR 89.9 per MWh on average). Gas prices currently sit at elevated levels and the outlook remains uncertain. Hence we applied 2 gas price scenarios in our electric/gas boiler trade-off, being EUR 200 and EUR 100 per MWh gas price. A final point is that the intermittency of renewables (remember the 26% load factor mentioned above) obviously implies that when opting for an electric boiler, the gas boilers act as back-up. A full electric set-up will basically imply sourcing energy in wholesale markets, which could be very expensive as the downtime in renewables tend to be will be felt through a higher spot price across the entire power market.
The table below shows the calculation and trade-off when going for an electric/gas boiler setting or sticking with the gas boiler setting. Under a EUR 200 per MWh gas price, the new electric & gas installation costs EUR 625mn in fuel costs, which is a whopping EUR 111mn in savings against the full gas powered installation. Essentially, RFC would be able to recoup its entire investment in one year and would still be left with EUR 35mn spare change. A go-ahead should make sense even at extraordinary high level of capital costs. Under a EUR 100 per MWh gas price, the financial benefit drops to EUR 20mn, but would still imply a reasonable 4year pay-back period on the investment, whereas the electric boiler has an economic lifespan of 15 years. Actually, the electric/gas combination breaks-even against the full gas combination at EUR 78 per MWh price for natural gas.
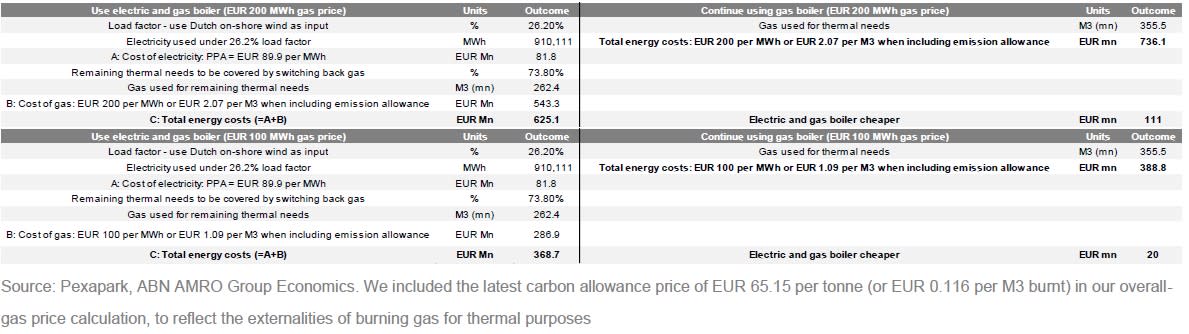
There’s more good news. Because of lower gas usage the electric/gas boiler combination saves roughly 26%(!) in carbon emissions as the electricity used comes entirely from renewable sources.
Our analysis is obviously based on simplistic assumptions. Perhaps RFC’s gas powered boilers are super-efficient and the energy content is much stronger that it would require less than 0.6 cubic metre per kg of carbon, which we use as a critical starting point of our analysis. Renewable wind power could under-perform on generation due to adverse weather conditions, by which the load factor drops and RFC would need to resort back to using more gas in its boilers. On the upside, replacing gas powered steam generators with electric steam generators in the energy intensive spray dying process could yield even larger financial and carbon reduction benefits. Our objective however was to show that under existing energy price levels, a switch to an electric boiler for the diary processing industry should immediately capture the attention of the plant’s Chief Financial Officer, but also the Chief Sustainability Officer.